how to make a 3d printed face shield
We are proud to support efforts to reduce the spread of the COVID-19 pandemic. We are providing a full set of 3D models and instructions for manufacturing your own face shield.
The core part of this model is based off of the awesome design by Budmen which has been clinically validated along with other NIH models. Our version is adapted for a velcro head strap instead of elastic.
This project should take you about 2 hours to print (depending on the 3D printer and settings) and about 10 minutes to construct, but if you make them in bulk, it should take less time per face shield.
1. MATERIALS
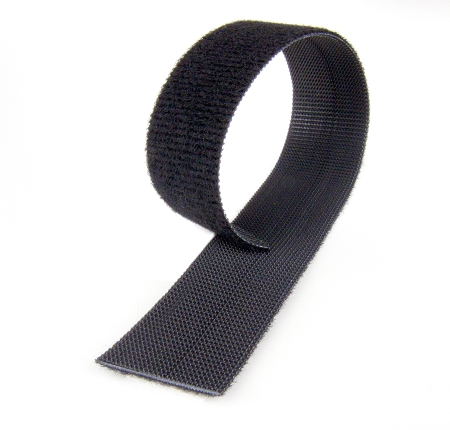
Double-Sided Hook & Loop Strap
The most popular brand is Velcro OneWrap, but we list several suppliers that make a similar product. Because it wraps around itself, it’s easily adjustable to any head diameter.
Width: 3/4″ (19mm)
Length: 30″ (762mm)
Suppliers
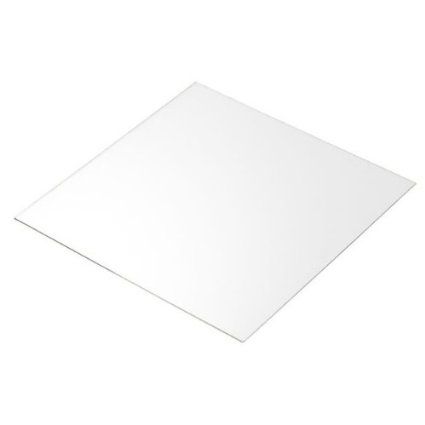
Acetate/Plastic Sheet
The main face shield is made of clear plastic sheets. The material that works the best is PETG, but if that’s not available–any clear plastic of the correct thickness will provide basic functionality.
Material: Any clear plastic
Size: 9″ x 12″
Thickness: Between 0.010″ to 0.030″ is ideal. We tested using 0.020″ and it worked very well. If you need the most inexpensive or plan to change the plastic sheets frequently, review the “thinner” sheet option below.
Note: Supply of this material is very limited, so the below links may not be available for purchase–but check other sites for availability.
Standard Thickness
- United States Plastics Corp – Vivak PETG Sheet
- Oasis Supply – Acetate Sheets
- Jekkis – Blank Stencil Sheets
Thinner Sheets
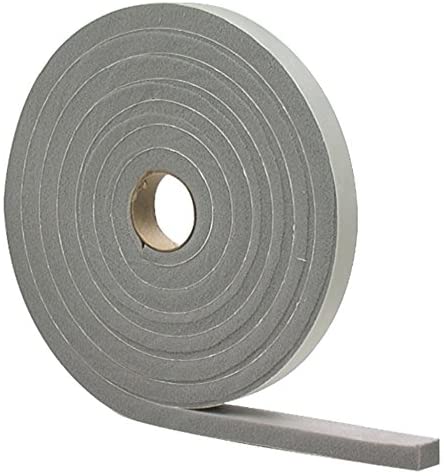
Adhesive-Backed Foam Strip
To comfortably rest on the forehead, you need a closed-cell foam thick enough to prevent as many air-gaps as possible.
Width: 3/4″
Thickness: 1/2″ is ideal, but can tolerate +/- 1/4″
Length: 11.7″ (~300mm)
Suppliers
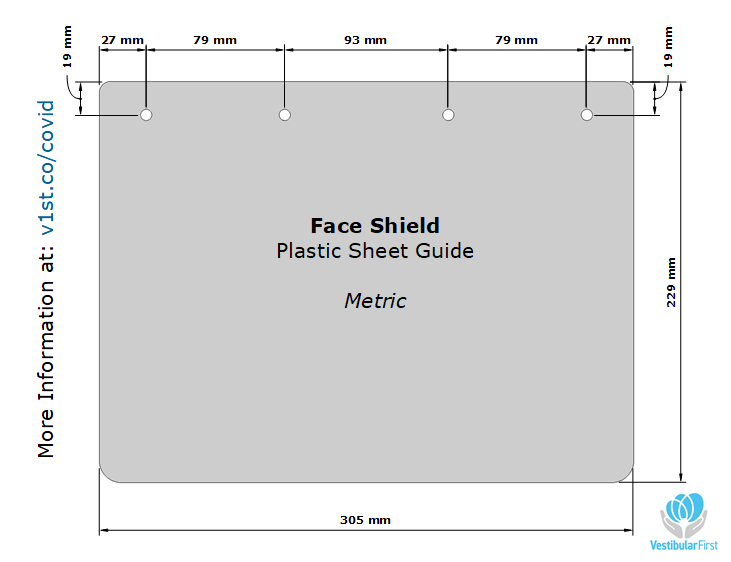
Printed Hole Guides
You will need to print out the hole punch template below at 100% original size (no printer scaling). This will allow you to punch the holes in the correct position
Hole Punching Guides
2. TOOLS
Rotary Cutter
It is unlikely that the plastic sheets will come exactly 9″ x 12″ and the easiest way to cut this is with a long metal ruler and a rotary cutter. Using plastic rulers and/or scissors will lead to inaccurate parts that can cause problems during construction.
Suppliers
- Fiskars Basic Rotary Cutter – This is the most basic cutter available
- Fiskars Rotary Cutter & Ruler Combo – This is great for perfectly straight cuts and when you also need a ruler.
Handheld 1/4″ Hole Punch
Standard 3-hole punches cannot get deep enough and usually cannot fit the larger sheets–so a handheld unit is the best. You need at least a 3/4″ throat on the punch to get the holes punch in the correct spot.
Suppliers
Corner Punch (Optional)
To properly finish off the exposed tips of the shield, the corners should be rounded. This step can be done with scissors, but for larger scale productions, a corner punch is a must-have.
If you can’t get a corner punch, you can use scissors to cut the rounded corners.
Suppliers
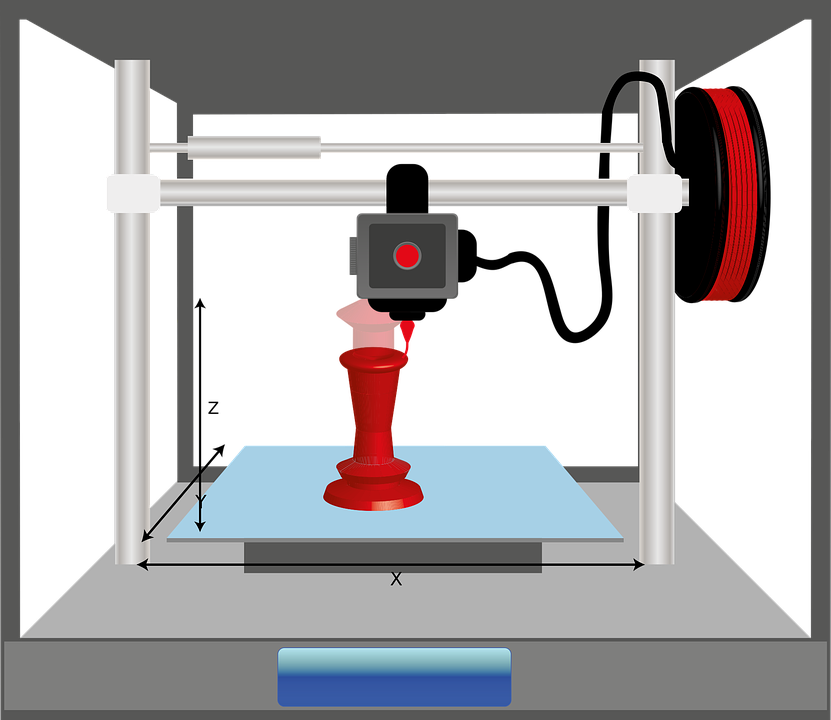
3D Printer
You will need access to a 3D printer that can print the model with the following minimum dimensions:
- Width: 125 mm
- Depth: 105 mm
- Height: 12.1 mm
If you aren’t able to find one, check out a service like Craftcloud. Use referral code REFN8KMEEQL to get 10% off your order! Our models are provided in millimeters and we recommend any basic plastic like PLA or SLA for a cost effective printing.
2. DOWNLOAD & PRINT MODEL
1.) Download
We have published our models on a 3D design site called Printables which allows people to collaborate and connect on projects. Please visit the Vestibular First 3D Models page to view this and our other 3D models.
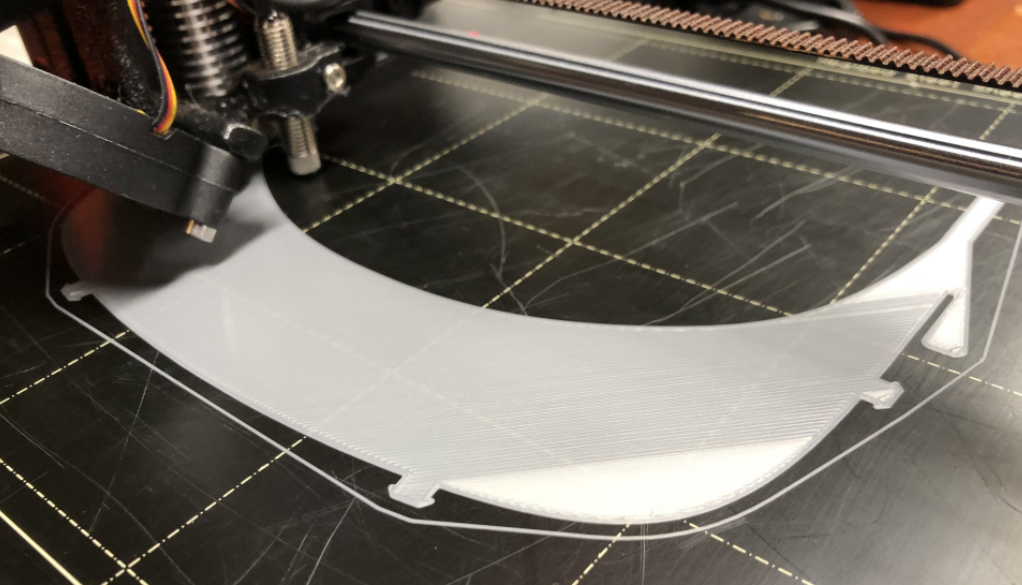
2.) Print Model
Here are the following settings we use for the the best output:
- Material: PLA
- Layer Height: 0.38 – 0.40mm
- Infill: 20%
- Infill Pattern: Rectilinear
- Outer Wall Line Count: 2
- Supports: None
3. CONSTRUCT FACE SHIELD
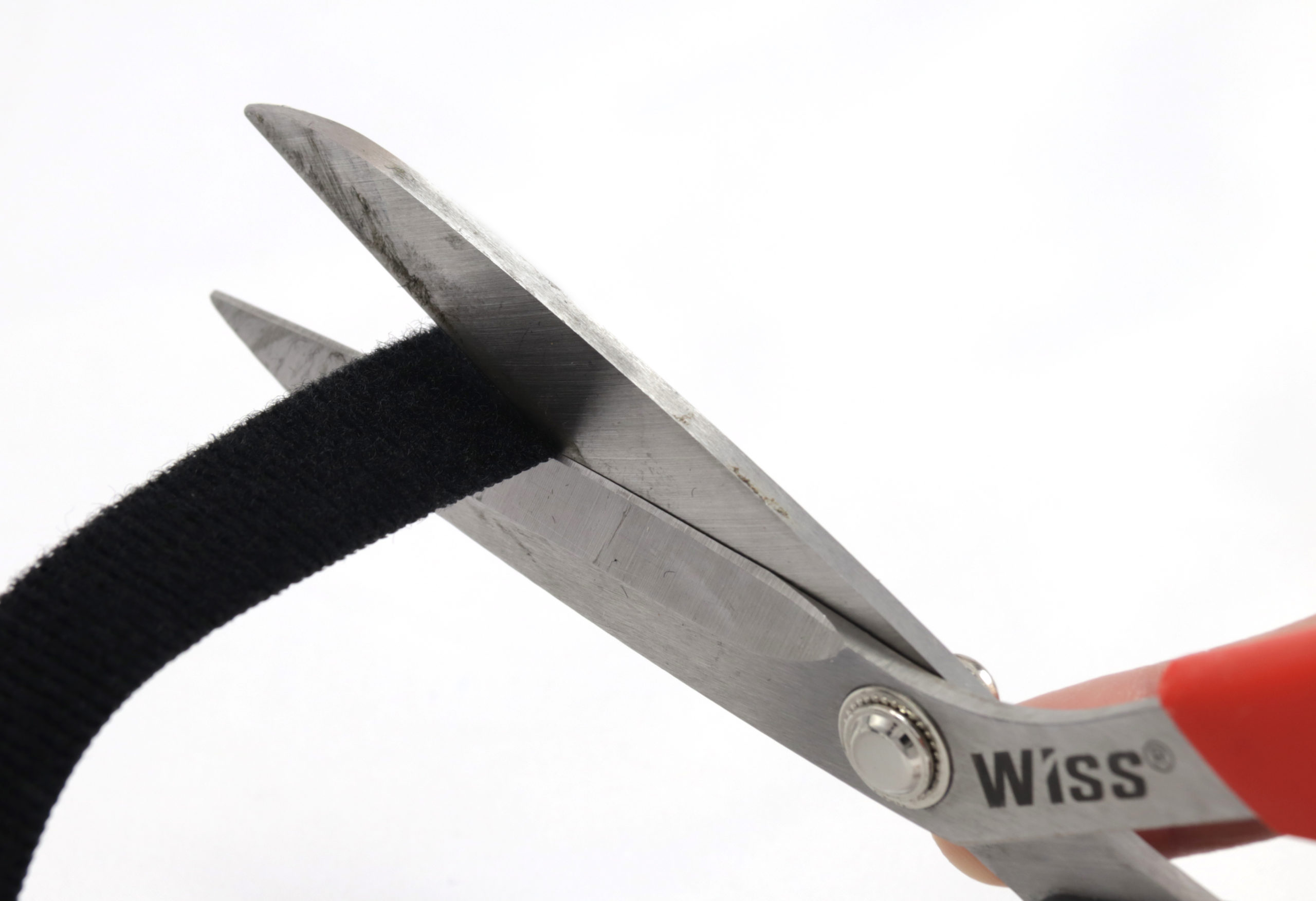
A.) Cut Head Strap
Measure out the 3/4″ double-sided hook and loop and cut tubing and cut:
- Length: 30″ (762 mm)
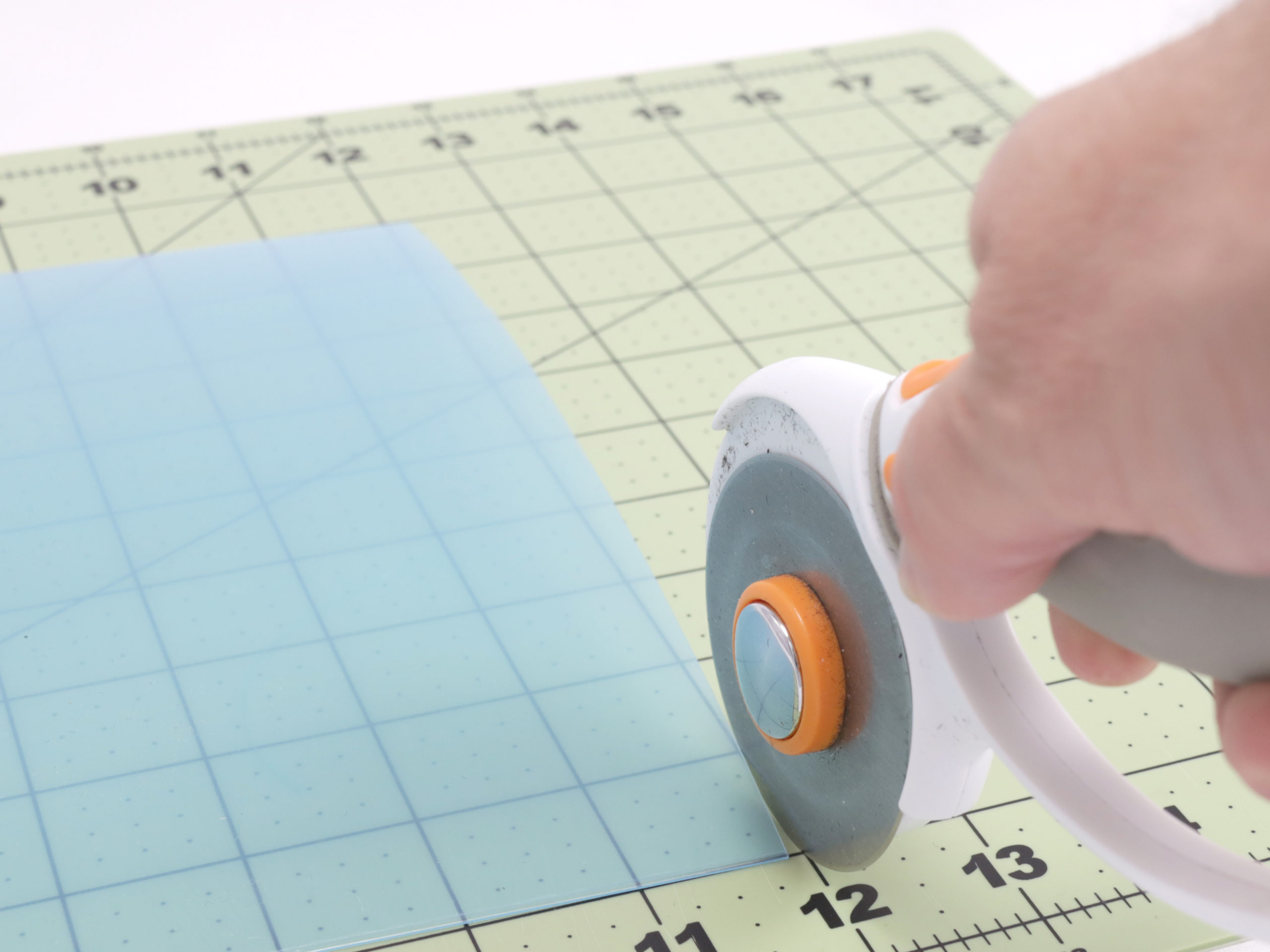
B.) Cut Plastic Sheet
Using a rotary cutter and a metal ruler, cut the plastic sheet:
- Length: 12″ (304mm)
- Width: 9″ (228mm)
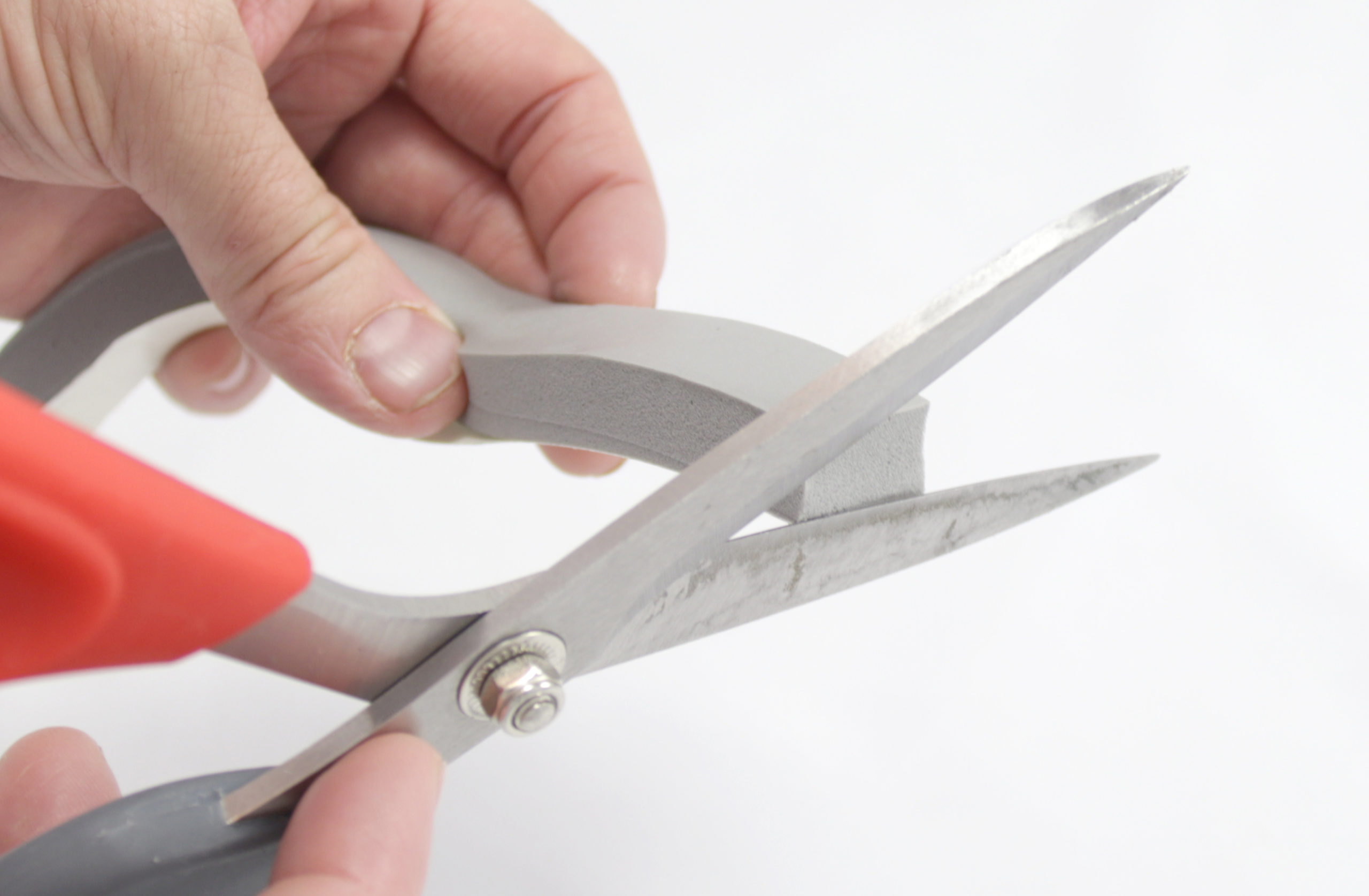
C.) Cut Forehead Cushion
Using scissors, cut the foam cushion while keeping the backing paper intact:
- Length: 11″ (280mm)
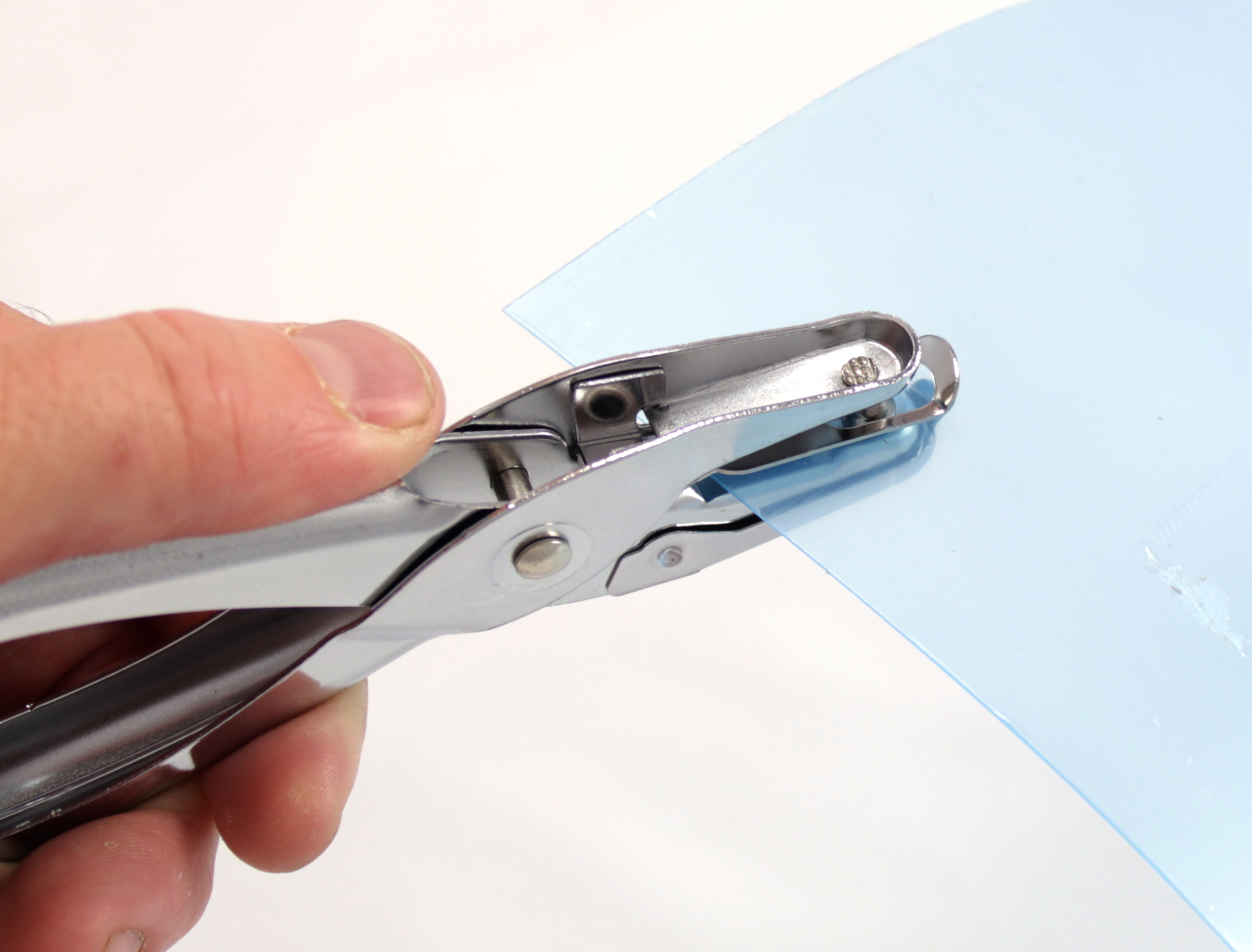
D.) Punch Holes in Plastic Sheet
Using your handheld hole puncher, punch 4 holes into the plastic sheet using the hole punch template as a guide
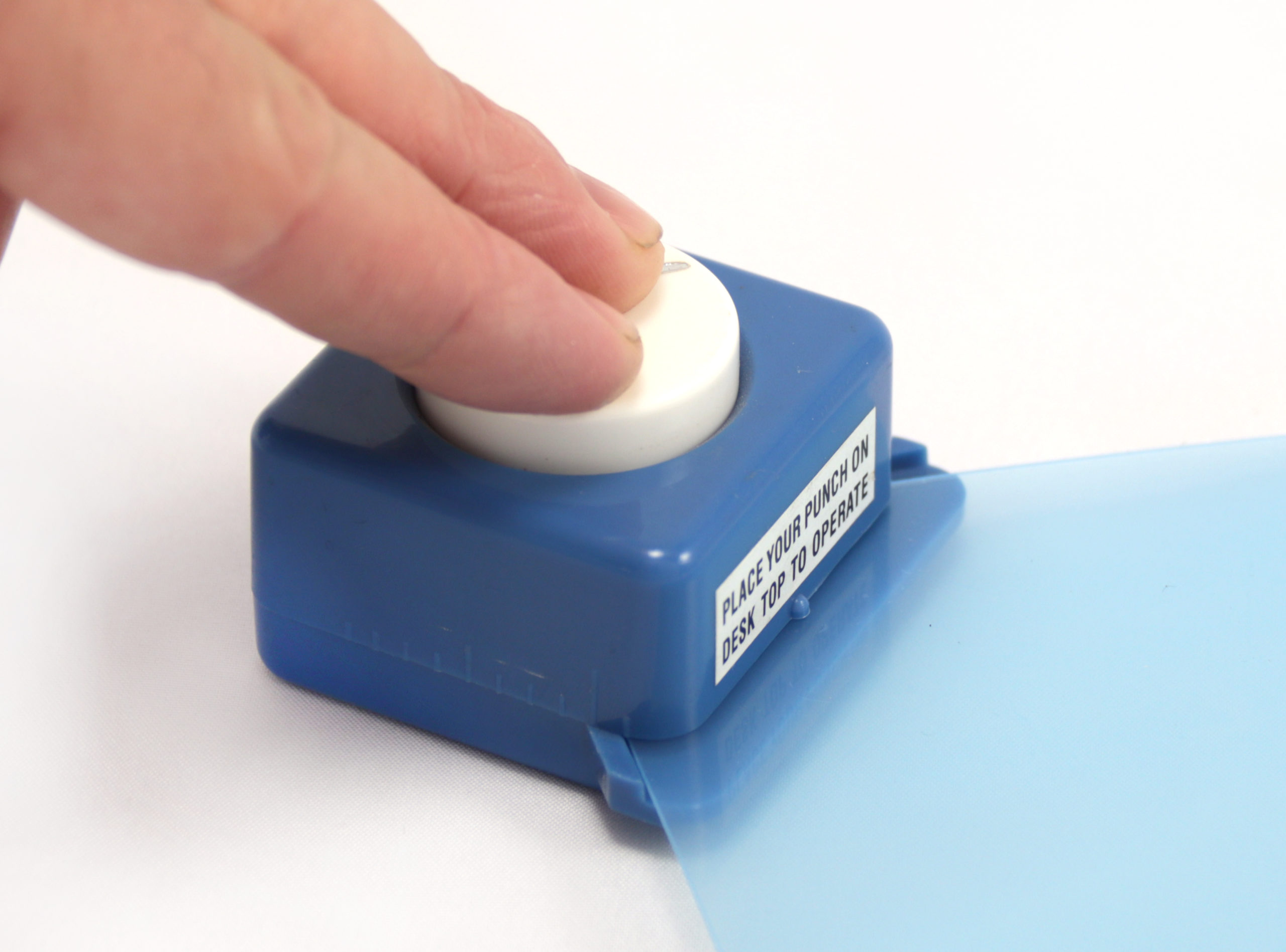
E.) Round Corners of Plastic Sheet
Using your corner punch (or scissors), round all 4 corners of the plastic sheet
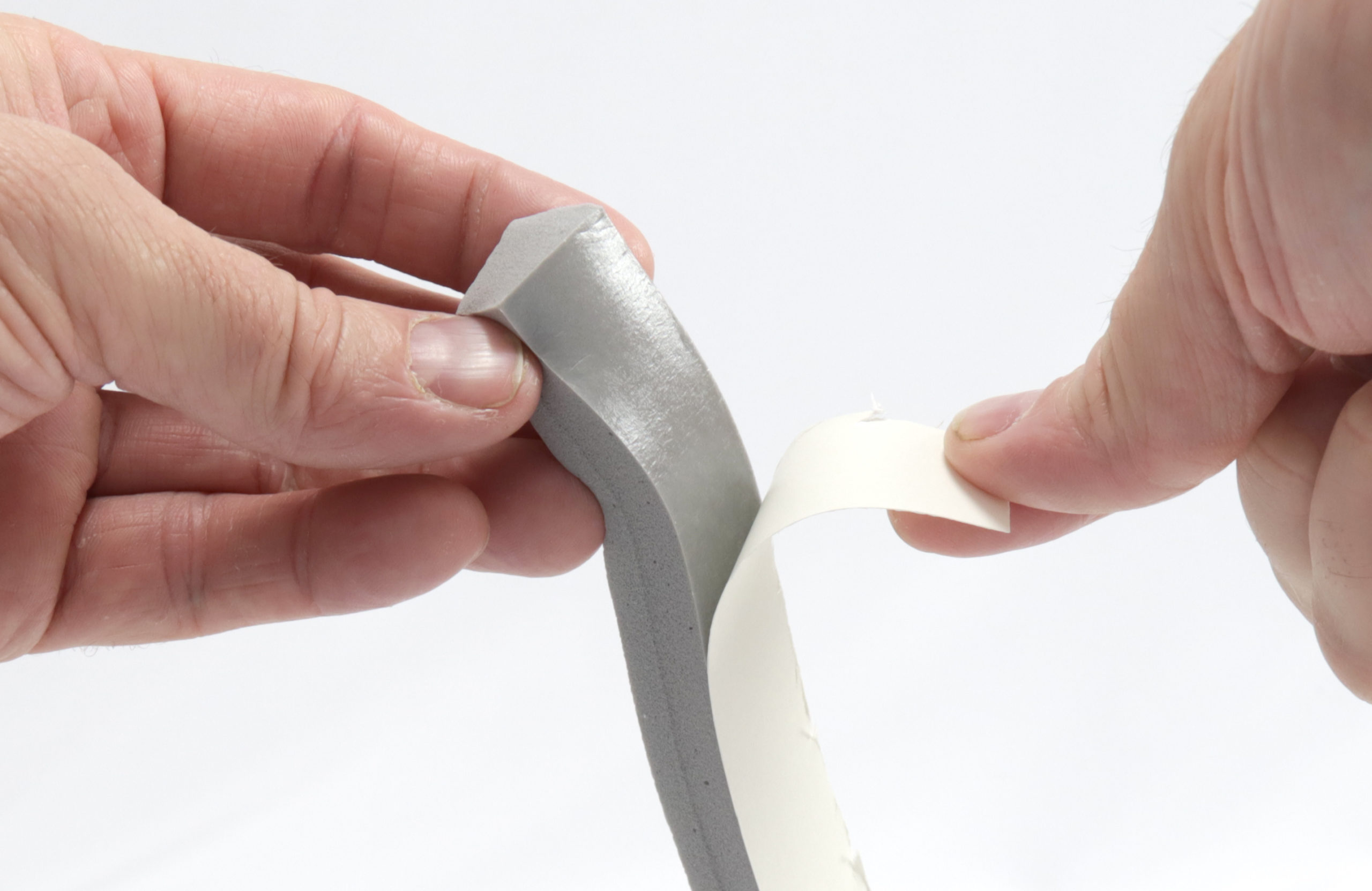
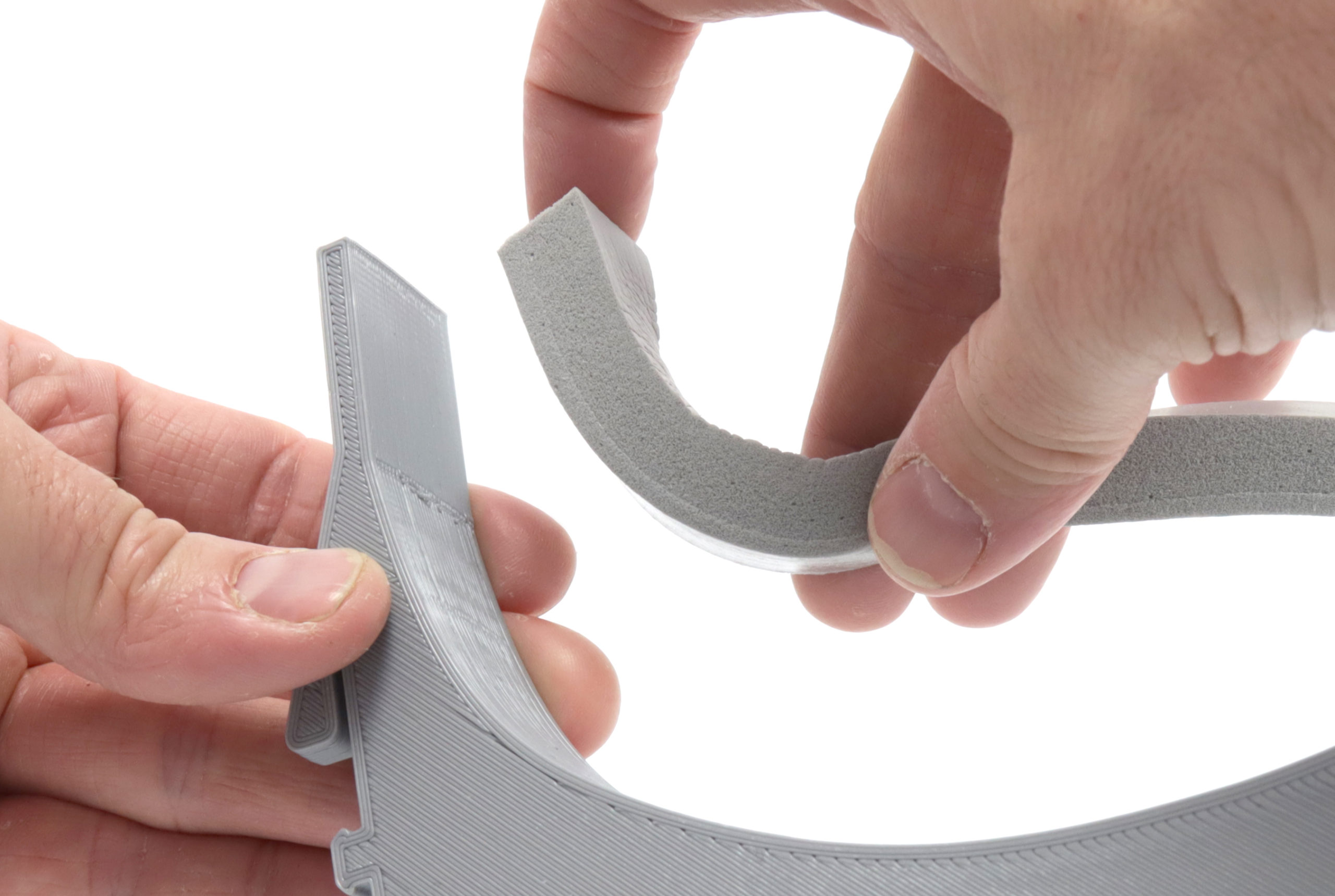
F.) Mount Forehead Cushion
- Peal pack the adhesive backing tape
- Press the sticky side firmly into face shield mount. Make sure adhesive is making full contact with plastic headset for best performance. If it’s not sticking reliably, try adding a small bead of silicone adhesive around the edges.
- Trim any excess foam with scissors
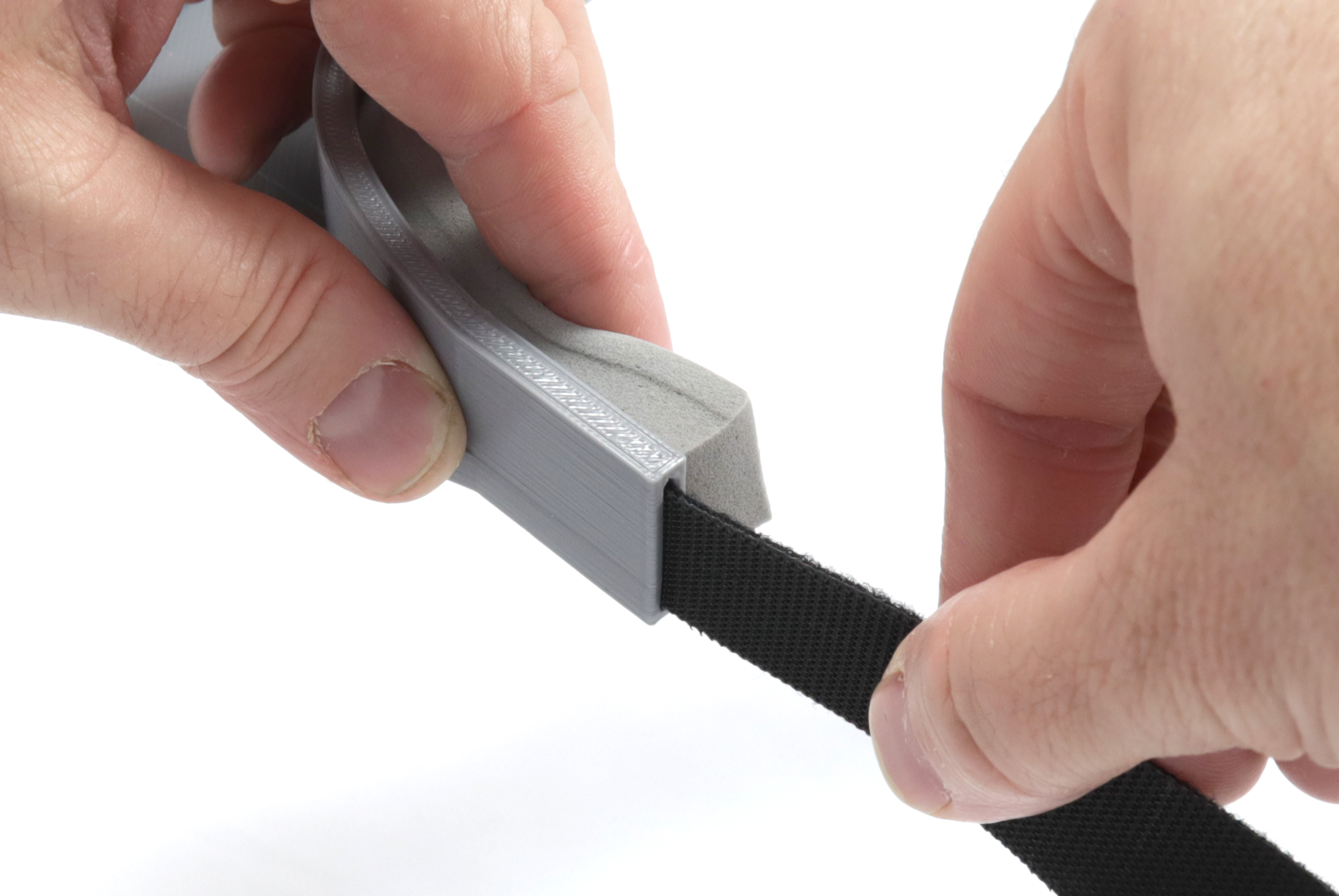
G.) Push Head Strap through Channel
Using your fingers, push the cut length of hook and loop strip through the channel found at the front of the face shield. Pull all the way through and make sure straps are even on both sides
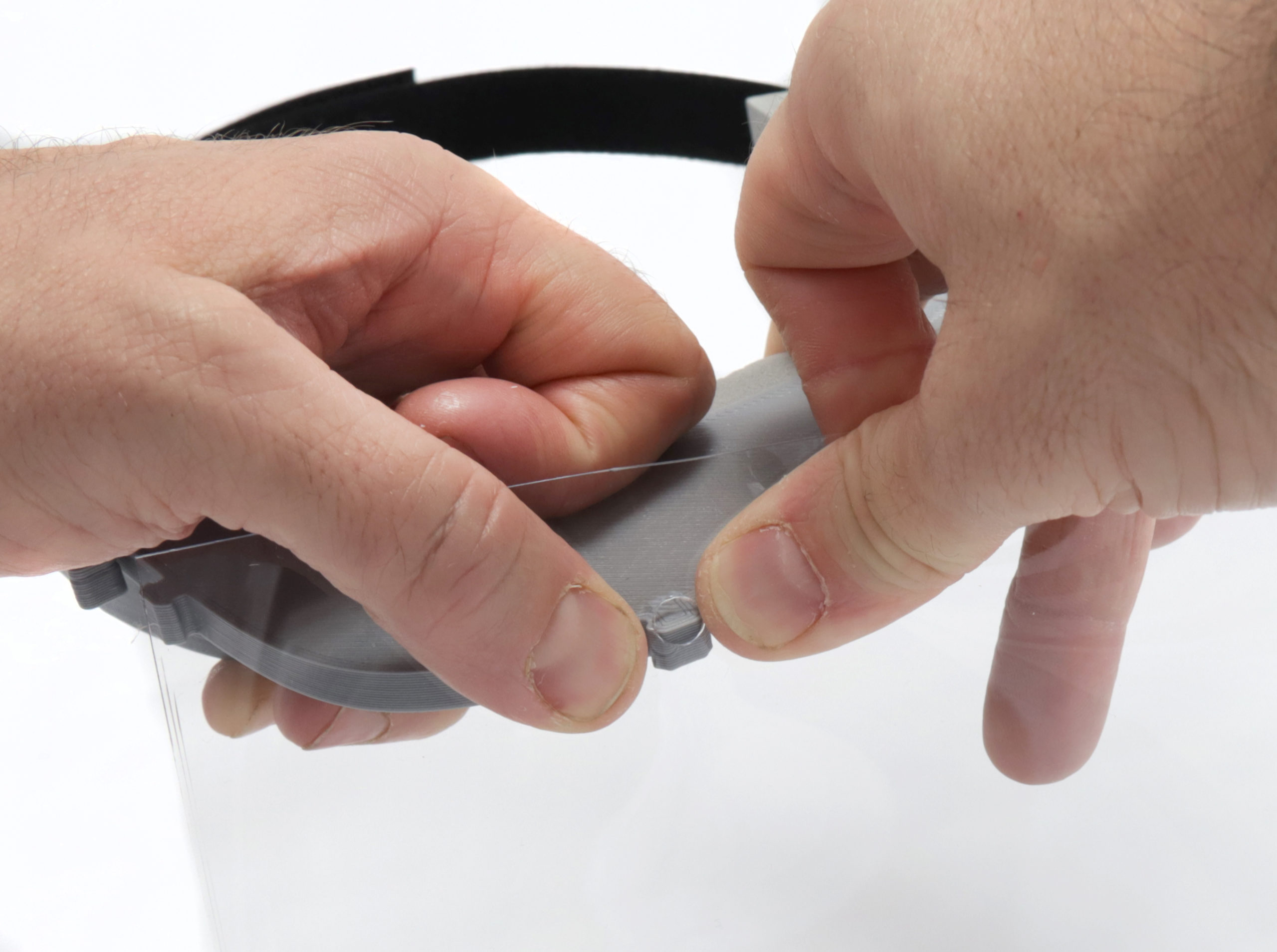
H.) Affix Plastic Sheet to Headset
With your fingers starting on one side, press the holes of the plastic into the “moorings” along the front of the face shield. Press the remaining holes into the face shield until fully secured.
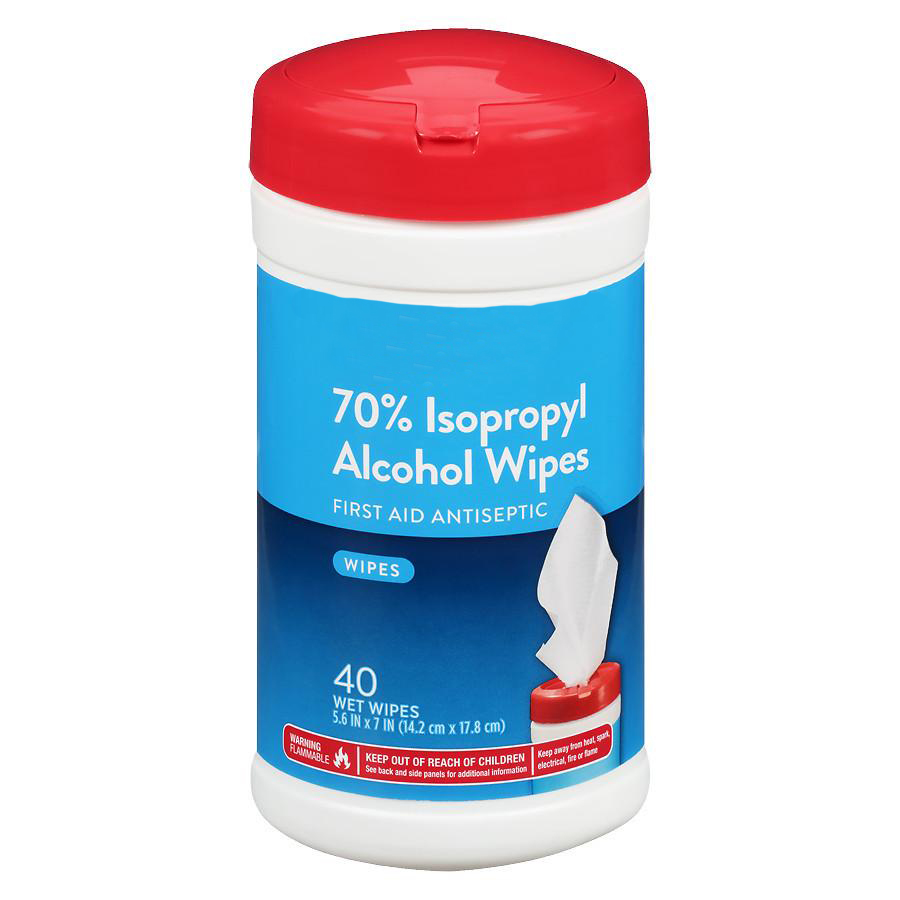
I.) Clean and Disinfect
Using disinfectant wipes or other antibacterial cleaner, make sure all parts are cleaned and ready for use. Do not use harsh chemicals on the plastic sheet to prevent it from getting scratched or cloudy.
Success!
Please share your success by letting our team know via Twitter, Facebook, or Thingiverse with a photo of your face! If you have ideas on how to improve the model or assembly, please let us know–we’re always open to feedback to make it better!